Imagine walking into a bustling printing or packaging facility. There’s a faint, chemical-like odor in the air, even if it’s well-ventilated. For the staff working there day in and day out, this odor is more than just a mild inconvenience; it’s a sign of potentially hazardous volatile organic compounds (VOCs) in the air. But how can facilities effectively manage and reduce these emissions without disrupting operations? This is where VOC catalysts come into play.
VOC catalysts are crucial in helping industrial facilities like those in the printing and packaging sectors meet environmental standards while improving indoor air quality for employees. But what exactly are VOC catalysts, and how do they work to make such a significant impact?
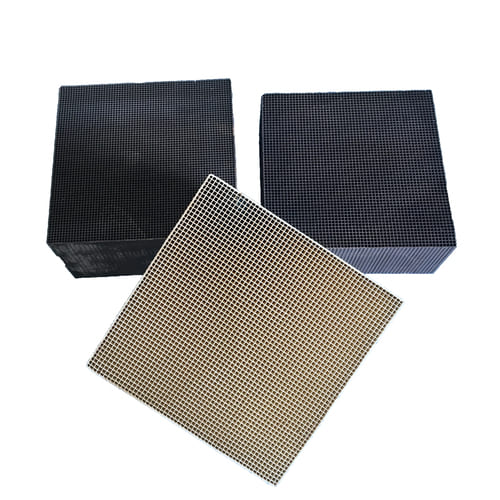
What Are VOC Catalyst, and How Do They Work?
VOC catalyst is materials designed to break down volatile organic compounds in industrial emissions. VOCs are chemicals that easily vaporize, releasing harmful gases into the air. These compounds can be found in various industrial processes, especially in printing and packaging where inks, adhesives, and coatings are prevalent.
VOC catalysts work by facilitating chemical reactions that convert harmful VOCs into harmless substances like carbon dioxide and water vapor. These reactions are typically oxidation processes, where VOCs are oxidized at relatively low temperatures, making them far more energy-efficient compared to traditional methods of VOC control like incineration.
This catalytic process allows for effective emission control while minimizing energy consumption, making VOC catalysts an environmentally friendly and economical choice for industries striving to reduce their carbon footprint.
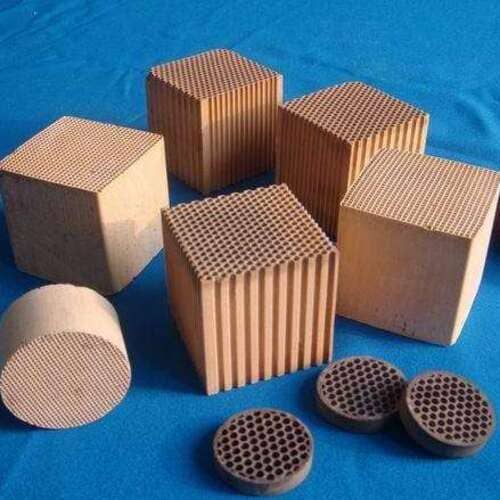
Why Are VOC Catalysts Important in Printing and Packaging?
The printing and packaging industries heavily rely on inks, varnishes, and adhesives, which are rich in VOCs. When these materials are used, they release VOCs into the air. Over time, these emissions can degrade indoor air quality, posing health risks for employees and environmental concerns for the community.
Using VOC catalysts can make a profound difference in such settings. By reducing harmful emissions directly at the source, they help facilities comply with strict environmental regulations and safeguard employee health. Moreover, VOC catalysts are often designed to work with low-temperature oxidation, reducing the need for additional fuel and energy, which translates into cost savings.
For printing and packaging facilities, VOC catalysts provide a way to balance productivity with environmental responsibility, improving air quality without slowing down production.
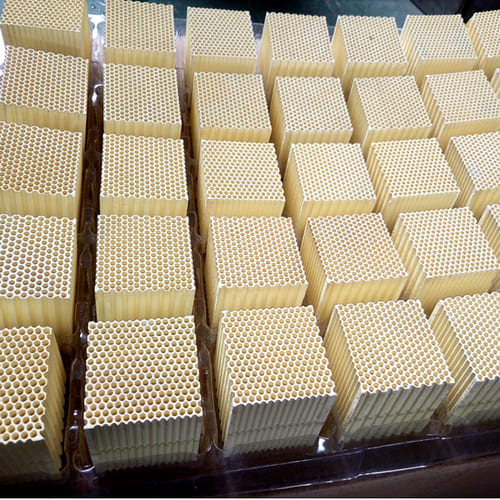
What Makes VOC Emissions Hazardous in These Facilities?
The health risks associated with VOC emissions in printing and packaging facilities are significant. VOCs contribute to respiratory issues, headaches, dizziness, and in severe cases, can lead to long-term health complications. Additionally, when VOCs are released into the atmosphere, they contribute to ground-level ozone formation, a major component of smog that affects air quality.
The environmental impact of VOCs goes beyond immediate health concerns. VOC emissions are linked to climate change, as some compounds can act as greenhouse gases. This creates an urgency for industries to reduce these emissions and adopt sustainable practices. VOC catalysts, therefore, play a dual role: protecting employee health and minimizing environmental impact.
How Do VOC Catalysts Improve Operational Efficiency?
Implementing VOC catalysts in printing and packaging facilities can actually boost operational efficiency in several ways:
- Energy Savings: Unlike thermal oxidizers, VOC catalysts do not require extremely high temperatures, leading to reduced energy consumption.
- Lower Operating Costs: Reduced energy usage translates directly to lower operating costs, making it a cost-effective solution for facilities.
- Extended Equipment Life: VOC catalysts help minimize the need for constant equipment maintenance due to clogging or excessive buildup of VOCs, extending the lifespan of other machinery involved in emissions control.
- Streamlined Compliance: Meeting regulatory standards is simplified, as VOC catalysts help facilities stay within legal limits for VOC emissions without requiring extensive operational changes.
By optimizing energy use and reducing wear on machinery, VOC catalysts help facilities maintain a more efficient workflow, ultimately improving both productivity and profitability.
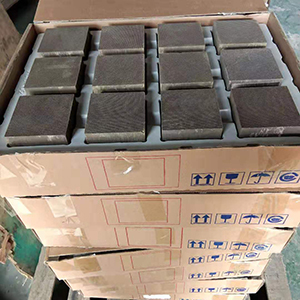
How Do VOC Catalysts Differ from Other Emission Control Methods?
While traditional methods like thermal oxidizers or carbon adsorption are effective at managing VOC emissions, VOC catalysts offer unique advantages:
- Lower Operational Temperature: VOC catalysts operate effectively at lower temperatures, significantly reducing the need for added heat and, consequently, energy consumption.
- Minimal Maintenance: VOC catalysts are low-maintenance solutions. Their design prevents the build-up that typically requires regular cleaning or replacement, unlike some other methods.
- Scalable and Versatile: VOC catalysts can be adapted to various sizes and operational demands, making them ideal for both small and large printing and packaging facilities.
In contrast, thermal oxidizers consume large amounts of energy, and carbon adsorbers require frequent replacement or regeneration. VOC catalysts provide a sustainable, long-term solution that combines high performance with low operational demand.
How Are VOC Catalysts Integrated into Printing and Packaging Facilities?
Integrating VOC catalysts into a facility is a straightforward process, often involving installation within existing ventilation systems or exhaust units. Once installed, VOC catalysts operate continuously to reduce emissions as processes take place.
Facilities have the option to implement different types of VOC catalysts based on their specific needs:
- Fixed-bed Catalysts: These are best for steady, continuous emissions, making them a good fit for larger facilities with consistent VOC output.
- Fluid-bed Catalysts: Ideal for fluctuating VOC emissions, as they can handle variations in air flow and VOC concentration, commonly seen in medium-sized facilities.
- Monolithic Catalysts: Known for their efficient surface area usage, they are often used in smaller facilities with strict space constraints.
Each of these setups can be optimized to capture and convert VOCs, enhancing air quality while allowing for operational flexibility.
Are VOC Catalysts Sustainable?
One of the most appealing aspects of VOC catalysts is their contribution to sustainable industry practices. By reducing energy requirements and cutting down on harmful emissions, VOC catalysts enable facilities to lessen their carbon footprint.
Additionally, VOC catalysts have a long lifespan(3-5years) and are resistant to deactivation, meaning they can remain effective for years. This reduces the need for frequent replacements and helps prevent waste, reinforcing sustainability in facilities committed to greener practices.
For companies in printing and packaging looking to enhance their environmental responsibility and align with corporate social responsibility goals, VOC catalysts are a valuable investment.
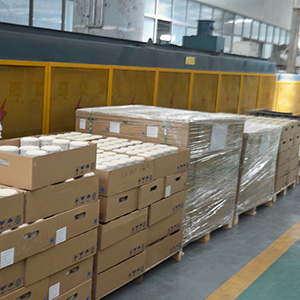
Conclusion
In the fast-paced world of printing and packaging, balancing productivity with environmental and employee health standards can be challenging. VOC catalysts offer an innovative solution to this dilemma. By converting harmful volatile organic compounds into harmless gases, these catalysts improve air quality, protect worker health, and contribute to global environmental efforts.
Incorporating VOC catalysts is a step forward for facilities aiming to enhance operational efficiency and reduce their environmental impact. As regulations tighten and the call for sustainable practices grows louder, VOC catalysts will undoubtedly play a key role in shaping the future of air quality in industrial settings.