Imagine if you will, a tiny particle, no bigger than a speck of dust, invisible to the naked eye but possessing the power to control chemical reactions. This isn’t science fiction; it’s the reality of monolithic catalysts. But how does the science behind these tiny powerhouses translate from laboratory conditions to full-blown industrial applications?
Monolithic catalysts, designed at the nano-scale, are the result of extensive scientific research. Their unique structure provides a massive surface area for chemical reactions, while their sturdy monolithic form allows for large scale industrial applications. The transition from the lab to the factory involves scaling up the production process, maintaining the catalyst’s quality and activity, and ensuring its performance under diverse industrial conditions.
Making the leap from the confines of a laboratory to the rigours of a factory environment is no small feat. Understanding how this transition is made helps us appreciate not just the complex science behind these catalysts, but also the remarkable engineering feats required to implement them in industry.
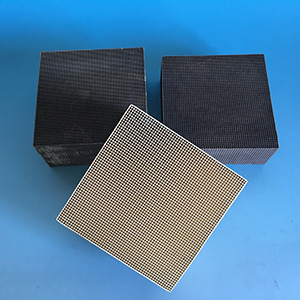
How are monolithic catalysts developed in a laboratory setting?
In a laboratory setting, monolithic catalysts are developed with meticulous precision. The base substrate is often made from ceramics or metals, offering durability and resistance to thermal shock. A thin layer of active material, often a precious metal, is applied over the substrate. This process, known as washcoating, maximises the surface area available for catalytic reactions.
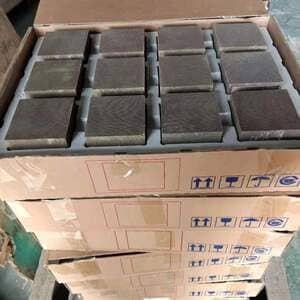
How is the manufacturing process of monolithic catalysts scaled up for industrial production?
Scaling up the manufacturing process is a challenge, as it requires maintaining the quality and activity of the catalyst while producing larger volumes. This involves precise control of the washcoating process to ensure a uniform distribution of the active material, as well as rigorous testing to confirm the catalyst’s performance at a larger scale.
How are monolithic catalysts applied in different industries?
Monolithic catalysts find applications across a range of industries, including automotive, chemical production, and energy. Their large surface area and high efficiency make them ideal for applications requiring high throughput, such as catalytic converters in cars or for controlling VOC emissions in industrial processes.
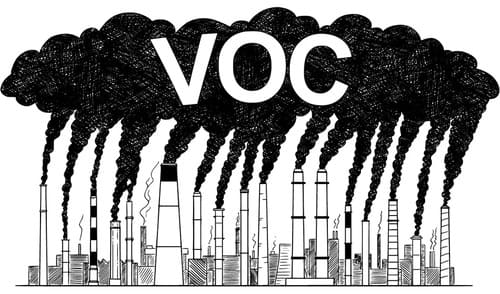
How does the science behind monolithic catalysts improve their industrial efficiency?
The science behind monolithic catalysts allows them to offer several advantages over other types of catalysts. Their structure maximises the available surface area for reactions, resulting in higher efficiency. Moreover, their physical form allows for high flow rates with low pressure drop, further enhancing their industrial usefulness.
Conclusion
In conclusion, the journey of monolithic catalysts from the lab to the factory is a remarkable demonstration of the seamless integration of science and engineering. It’s a testament to the power of scientific understanding, precise engineering, and meticulous quality control in bringing a product from the microscopic world of a laboratory to the grand scale of industrial applications.