The question might have stroked one’s mind a thousand times: why does it happen that in vehicles or at an industrial level, the catalysts are coated on ceramic honeycombs? Why does this apparently simple design become so crucial with regards to efficiency? Is it all about maximizing surface area, or is there something more to it? Ceramic honeycombs have played a great role in developing the performance of many catalytic processes, among them being automotive exhaust systems. But what’s so special with this combination? Let’s get in and find out why honeycombs made of ceramics act as a substrate for catalytic coating.
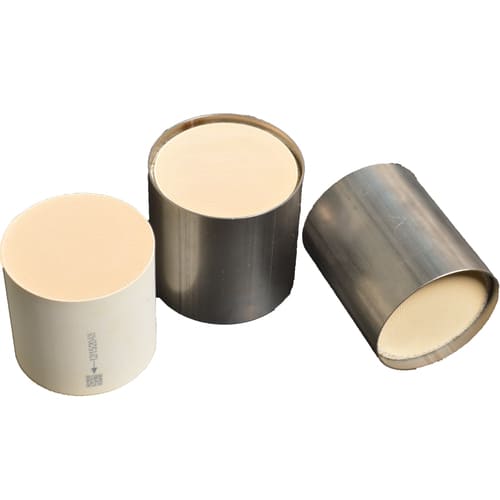
What is a Catalyst Coated Ceramic Honeycomb?
One of the major components in most of the emission control systems that also include diesel particulate filters and catalytic converters is the catalyst-coated ceramic honeycomb. The honeycomb substrate is made of ceramic. The ceramic, in itself, is so constructed that it provides a setting which maximizes the surface area for chemical reactions. Then, the catalyst acts to convert all harmful gases, such as CO, NOx, and HC, into less harmless gas substances like CO2 and H2O. It is this combination of ceramic and catalyst that provides an efficient and durable system to bear high temperatures and corrosive conditions. The unique structure of the ceramic honeycomb helps to disperse the gases over the catalyst’s surface to make the chemical reactions take place in a more effective manner. Without this coating, the catalyst would not work satisfactorily.
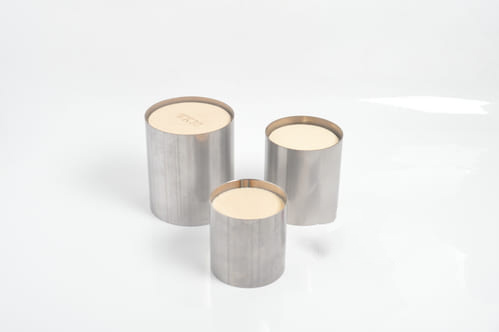
Why is Ceramic Used for Catalysts?
The most suitable ceramic materials for catalytic applications are Al2O3, SiC, and cordierite. All these materials are suitable for such extreme operating conditions due to their high thermal stability, mechanical strength, and resistance against chemical erosion.
High Thermal Stability of Ceramic Honeycomb
Resistance under such high temperature-It also will be suitable for applying into the automobiles because these materials show resistance under extremely high temperature. As in diesel engine-like, temperatures range up to 800° C higher the ceramic substrates show such kind of high resistance and holds the ability of the catalyst since the start of its functional life.
Honeycomb Structure
Besides, the surface area increases intrinsically because the nature of the ceramic honeycombs is intrinsically porous; thus, this is where the catalytic reactions occur on the catalyst surface. The greater the surface area, the more effectively such reactions can occur. A honeycomb structure allows gas to pass through a wide network of small channels in which it can interact far more effectively with the catalyst.
Lightweight and Durable
While tough, ceramics are relatively lightweight for metals with similar thermal resistance; this constitutes a strong advantage in automotive applications where weight is critical with regard to fuel efficiency. Toughness of the ceramic materials involved ensures the honeycomb structure will not degrade during operation over the life of an engine.
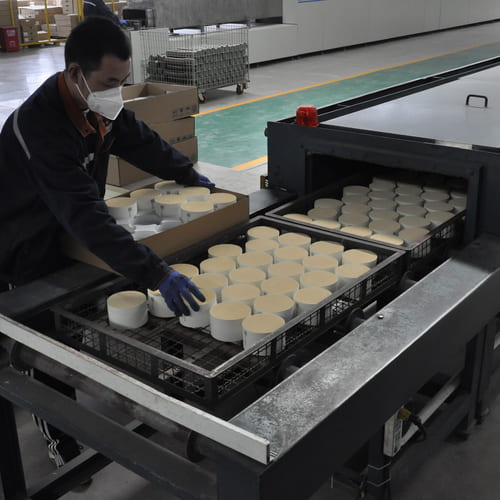
How Does the Catalyst Coating Work?
The catalyst coating is a thin layer containing precious metals such as Pt, Pd, and Rh that possess excellent catalytic properties. All these metals are deposited on the surface of the ceramic honeycomb by several different techniques, including the use of washcoating. This process deposits the metals on the porous surface of the ceramic, thus making the coating area very large.
Coated, the catalyst assists in the chemical reaction of the pollutants being converted to less harmful emissions. In a typical example of a three-way catalytic converter, platinum and palladium act to reduce NOx to nitrogen (N2) and oxygen (O2); similarly, rhodium works in reducing CO and hydrocarbons into CO2 and water.
Efficient Gas Flow and Contact
Another reason why this honeycomb design works so well is because of the facility of gas flow through it. The structured design ensures that the gases pass through all catalytic surface areas, providing the best conditions for chemical reactions. The gas does not just pass over the surface but rather flows through a dense network of channels such that all the gas comes into contact with the catalyst.
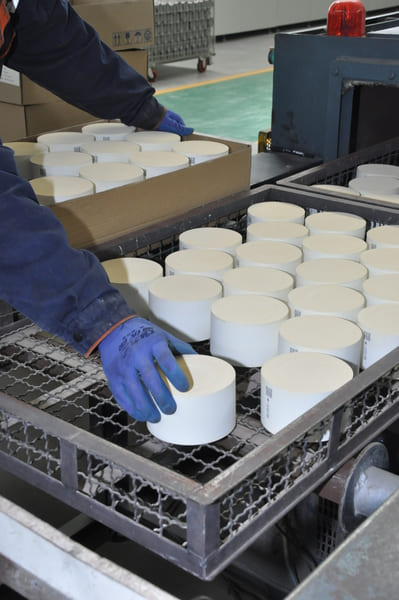
The Role of Honeycomb Shape
Why would it adopt this shape from having a flat surface? It does this because while the surface area is maximized, its volume is minimized. Basically, a honeycomb contains several hexagonal cells which are parallel and thin-walled. In such a way, this design maximizes exposure of the gases to the catalytic surface while keeping the size of the substrate compact. The honeycomb structure minimizes the flow resistance of exhaust gases for good performance of the engine.
The honeycomb structure has channels that are carefully sized to optimize the contact time between the exhaust gases and the catalyst. It is this balance between surface area, gas flow, and reaction time that makes the catalyst-coated ceramic honeycomb so effective.
How Does Coating Improve the Catalytic Process?
The coating on the ceramic substrates is thus the most critical link in the chain of current technologies that is used for emission control. Ever since the catalyst coated the honeycomb of ceramics, this system improved a thousandfold concerning emission conversion to less toxic gases. Only then did vehicles finally meet stringent standards and cut down on footprinting in nature.
Besides, the use of ceramic as the base material makes the system more durable to resist such high thermal and chemical stresses imposed in an automotive environment. Because the catalyst coating ensures efficient operation of the system over longer periods, replacements or maintenance will have lower frequency.
Cost-Effectiveness
Although platinum, palladium, and rhodium are very expensive as precious metals, the use of ceramic substrates allows the application to be rather inexpensive. Since the surface area has been maximized, less precious metal is required for the same catalytic effect. The system is therefore more efficient but also much cheaper in the long term.
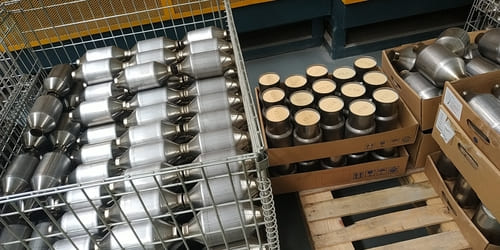
Conclusion
Ceramic honeycombs coated with catalysts are a very important part in most of the catalytic processes involved, especially in emission control.
The combination of high surface area ceramic structure and the catalyst coating has allowed efficient conversion of harmful emissions into less harmful substances. The ceramic base offers great thermal stability and durability while the honeycomb design provides equal distribution of gases across the catalyst’s surface. Put together, these provide a system much more helpful for pollution reduction, besides being low in cost and long in durability. Understanding why catalysts are coated onto ceramic honeycombs in the first place gives even greater appreciation for this technology that has made modern vehicles and industrial processes so much friendlier to the environment.