Why is one type of catalytic converter more effective than another? Why do some catalytic filters have different configurations from one to the next? Is there a distinguishing characteristics between a monolithic catalyst versus a ceramic honeycomb?
A choice between monolithic catalysts and ceramics in honeycomb would somewhat leave one perplexed. To begin with, while either is a very vital part of the emission control system, they have some structural or functional differences. These differences, however, will be well understood only when one looks into application and performance in various circumstances.
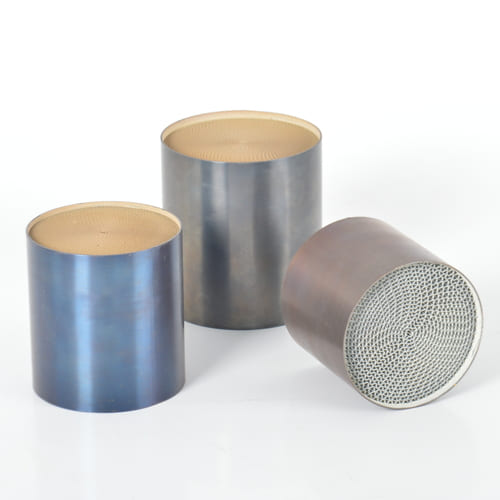
What is Monolithic Catalyst?
A monolithic catalyst is a type of catalytic converter wherein the base structure itself is made up of one single unit that is solid and consists of materials made up of either ceramic or metallic materials. Other forms include ceramic honeycomb, etc., wherein older versions had thousands of passageways, yet even this was solid and hence allowed less space between them for the gas to move through it.
The function of a monolithic catalyst in the case of emission control is based on the use of mentioned noble metals like platinum, palladium, and rhodium to catalyze such chemical reactions that lower harmful pollutants content in exhaust gases. Gas passes through a monolithic structure and reacts with the metals present; it results in harmless emissions, such as carbon dioxide and water vapor.
Probably one of the advantages of the durability involves the nature of monolithic catalysts. Since they are of solid nature, there is less chance of breakage and blockage; hence, they are completely apt for heavy-duty machinery of industries or big-size vehicles.
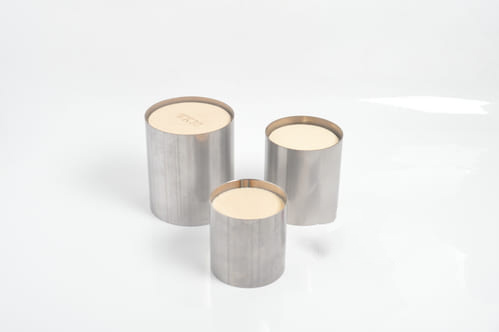
What is a Ceramic Honeycomb?
Contrasting the metal corrugated structure, the ceramic honeycomb represents one of the traditional types of structure in this direction finding wide applications in a big number of catalytic converters. The honeycomb structure represents high-temperature-resistant material for example, cordierite, and is characterized with a lot of passageways. The small-size channel gives an extended area to the contact of the exhaust gas with the active metals of the catalyst. Further on, the design promotes an efficiency of the catalytic process.
The main advantage of the ceramic honeycomb is that it can provide a large amount of catalytic material in a small area. Thus, an increased interaction time between the exhausting gases and catalysts, hence better conversion of the pollutants. On the other hand, under conditions of sudden change in temperature or excessive pressure, such ceramic honeycomb structures remain more fragile compared to their counterparts of monolithic catalysts.
Hence, ceramic honeycomb finds wide applications in automobiles and light-duty applications where the space is not very vast yet high catalytic efficiency is necessary.
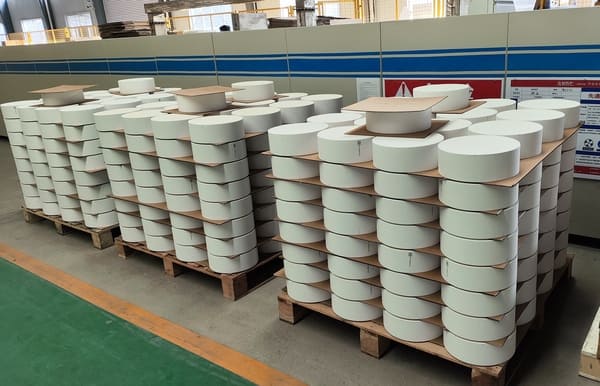
Basic Differences Between Monolithic Catalyst and Ceramic Honeycomb
Now that we basically know both, let us break it down into pieces as key differences between the two.
1. Structure and Material:
- Monolithic Catalyst: A monolithic catalyst generally employs a solid ceramic or metallic structure. It is more compact and solid in design.
- Ceramic honeycomb is a type of grid, multi-channel structure with larger area for catalytic reactions. Its main preparation materials are those from ceramic groups such as cordierite and alumina.
2. Durability:
- The monolithic catalyst is generally stronger and able to bear higher mechanical stresses and thermal shock.
- On the other hand, it is true that the ceramic honeycomb may be a bit fragile, particularly with changes in temperature or impacts in general.
3. Efficiency
The nature of its design makes the area surface coverage higher in ceramic honeycomb. It increases interfacing of the exhausts with the catalyst and hence makes a compact-sized system efficient.
- Monolithic catalyst: Although strong, and sometimes reduced in surface area, hence minutely less catalytically efficient, it makes up with long life and bearing wear and tear.
4. Applications:
- Large-scale industry or heavy-duty transportation requiring durability represents some of the important applications for monolithic catalysts.
- Ceramic honeycombs are in greater usage either in the case of small vehicles or when small-sized, efficient catalysts are desired.
5. Cost:
Manufacturing-wise, considering materials and their processes, the monolithic catalyst is expensive to fabricate, once again considering precious metals application.
Ceramic honeycomb constructions are generally less involved and less costly to manufacture and thus can be used far more widely in higher volume applications.
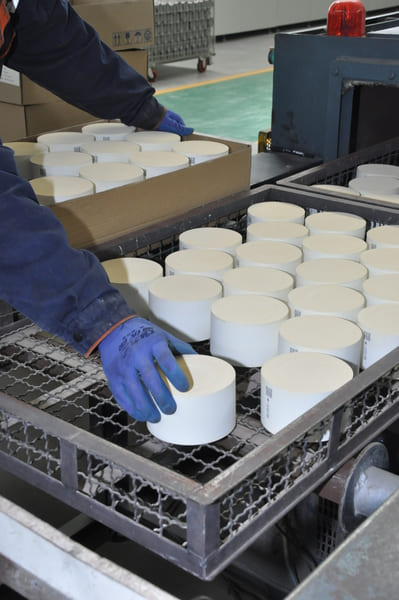
Why Does the Structure Count in Emission Control?
The structure plays a significant role in the overall effectiveness of catalysts. For instance, the larger the surface area is, the greater the opportunity the exhaust gases have to reach and come into contact with more amounts of the catalytic material, hence increasing the chance for reduction of the pollutants.
For the exact same reasons discussed above, a monolithic catalyst provides a strong and robust backbone or skeleton that would stand the test of many years even if stress in the catalyst and or sudden temperature fluctuation are experienced continuously.
More Related Questions
1. Does Monolithic Catalyst Have an Automotive Application?
Yes, though the monolithic catalyst finds wider industrial applications, they could also be found in automotive exhaust systems, mainly in large vehicles or those which are required to have more toughness.
2. Is the ceramic honeycomb more effective than the monolithic catalysts?
Generally speaking, ceramic honeycombs would have a higher surface area and may provide marginally better efficiency in converting emissions. In some applications, the durability and robustness of monolithic catalysts might prove more advantageous.
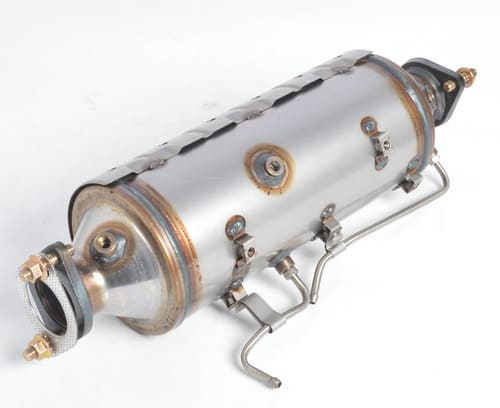
3. How does the design affect the environmental performance?
The overall environmental performance of the catalyst depends on its capability for reduction of the following: nitrogen oxides (NOx), carbon monoxide (CO), and hydrocarbons (HC). Both kinds of catalysts, monolithic catalysts, and ceramic honeycombs are capable of giving high levels of pollutant reduction, but the structure chosen may affect the rate of conversion.
4. Are these types of catalysts recyclable?
Both types of catalysts can be recovered, but recovery from monolithic catalysts may be considerably more difficult because of the sophistication in the solid structure. In both monolithic and ceramic systems, the precious metals are usually recovered for re-use in the production of new catalysts.
5. Which one should I use in my vehicle or equipment?
Basically, depending on your needs, it is either the monolithic catalyst or the ceramic honeycomb. For one that is strong and durable enough to be used in big vehicles or heavy machinery, monolithic catalysts are considered outstanding. More high-efficiency, compact, and lighter applications are where a ceramic honeycomb may be suggested, with passenger vehicles in mind.
Conclusion
The conclusion goes to the relative merits of the monolithic catalyst and the ceramic honeycomb in emission control. Monolithic catalysts provide durability and long life and, hence, fit best for heavy-duty applications. On the other hand, the ceramic honeycomb provides a much higher surface area for effective efficiency in compact systems but is rather fragile. Understanding the key differences between these two technologies will help you make the best choice for your needs in emission control.