Have you ever wondered how honeycomb zeolite, a new type of molecular sieve material, is produced? What makes it so special compared to other molecular sieves? Why is it gaining traction in adsorption separation, catalytic reactions, and gas storage?
Honeycomb zeolite, composed mainly of silicon, aluminum, oxygen, and other metal cations, stands out due to its large pore size, high specific surface area, excellent thermal stability, and chemical stability. In this blog, we will delve into the three primary methods of producing honeycomb zeolite: wet method, gas phase method, and hydrothermal method. Each method has its own set of steps, advantages, and disadvantages, which we will explore in detail.
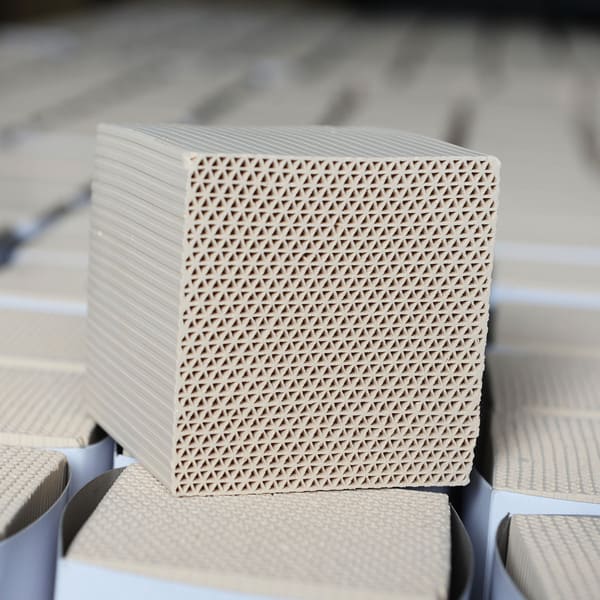
What are the Common Production Methods of Honeycomb Zeolite?
Wet Method: The wet method is a traditional approach to creating molecular sieves. The process involves adding zeolite seeds to a raw material solution containing the appropriate concentration of aluminosilicate. Through a series of treatments and crystallization processes, a honeycomb zeolite molecular sieve is formed.
Advantages:
- Large preparation scale
- Low equipment cost
- Easy control
Disadvantages:
- Long crystallization process
- Extended preparation cycle
The wet method’s simplicity and cost-effectiveness make it suitable for large-scale production, although the lengthy process may be a drawback.
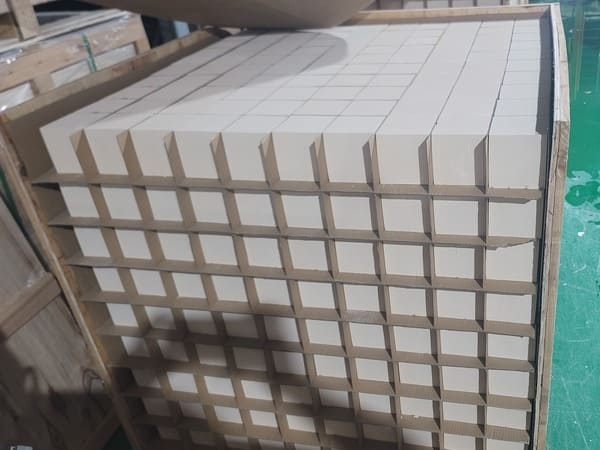
Gas Phase Method: The gas phase method, a more modern approach, involves two primary techniques. The first technique directly reacts ethyl silicate and octadecyltrimethylammonium (CTAB) at high temperatures to produce nanocrystalline seeds. The second technique involves the calcination and heating of these nanocrystalline seeds under controlled chemical reaction and thermodynamic conditions to form a honeycomb structure.
Advantages:
- Short reaction time
- Small and uniform crystal size
- High specific surface area
- Honeycomb structure
Disadvantages:
- High control difficulty
- High equipment cost
The gas phase method’s ability to produce uniform crystals quickly is a significant advantage, despite the challenges in process control and higher equipment costs.
Hydrothermal Method: The hydrothermal method mixes silicic acid and aluminic acid with templates and crystallizers in a high-temperature and high-pressure environment to form zeolite molecular sieves. This method allows for the adjustment of pore size by selecting different crystallizers and templates, resulting in a higher cracking degree compared to hollow spheres.
Advantages:
- Shorter preparation time than the sol-gel method
- Ability to produce large quantities of spherical or irregular honeycomb zeolite sub-sieves
- Optimizable crystal properties and morphology
Disadvantages:
- Requires high-temperature and high-pressure conditions
- Need for precise control of reaction conditions and additives
The hydrothermal method’s versatility in adjusting pore sizes and optimizing crystal properties makes it highly effective, although it demands rigorous process control and specific conditions.
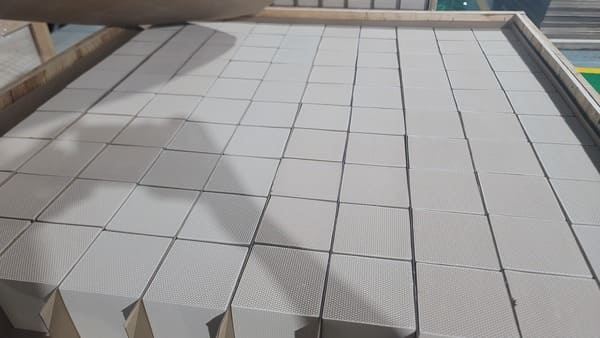
How Do These Methods Compare in Practical Applications?
Wet Method Questions:
- Why is the wet method still relevant despite its long preparation cycle?
- How does its ease of control benefit large-scale production?
The wet method remains relevant due to its simplicity and cost-effectiveness, which are crucial for large-scale industrial applications. Its manageable process controls ensure consistent quality, making it a reliable choice despite the longer production time.
Gas Phase Method Questions:
- What makes the gas phase method advantageous for producing uniform crystals?
- Why is the high control difficulty considered a disadvantage?
The gas phase method’s ability to produce small, uniform crystals quickly is a significant advantage for applications requiring precision. However, the need for precise control over reaction conditions makes it a challenging method, increasing the risk of inconsistencies and higher production costs.
Hydrothermal Method Questions:
- How does the hydrothermal method’s ability to adjust pore sizes impact its applications?
- What are the challenges of maintaining high-temperature and high-pressure conditions?
The hydrothermal method’s capability to tailor pore sizes enhances its applicability in various fields, such as gas storage and catalytic reactions. However, maintaining the necessary high-temperature and high-pressure conditions requires sophisticated equipment and precise process management, posing significant challenges.
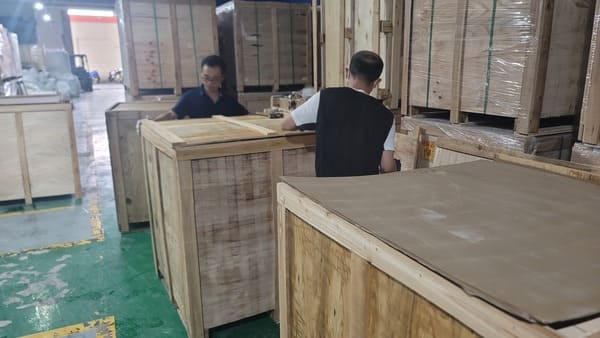
Conclusion
Understanding the production methods of honeycomb zeolite highlights the material’s unique properties and applications. The wet method, gas phase method, and hydrothermal method each offer distinct advantages and face specific challenges. The choice of method depends on the desired properties of the zeolite, production scale, and cost considerations.
Honeycomb zeolite’s versatile applications in adsorption separation, catalytic reactions, and gas storage underscore its importance in various industries. By mastering the production techniques, manufacturers can optimize the material’s performance, driving innovation and efficiency in their applications.