Have you ever wondered how monolithic catalysts are produced and what happens to them once they’ve served their purpose? How long does a monolithic catalyst typically last? What measures can be taken to ensure its safe disposal? To understand the importance of these catalysts in the industrial world, we must trace their lifecycle from production to disposal.
Monolithic catalysts undergo a carefully controlled lifecycle, from their creation, through their operational use, to their final disposal. Each stage requires meticulous planning and implementation, ensuring that the catalysts perform at their best while minimizing environmental impact. With their robust and efficient design, monolithic catalysts offer several advantages over other types of catalysts, including a longer lifespan and greater ability to withstand extreme conditions.
Understanding the lifecycle of monolithic catalysts can give us insight into their sustainability and impact on our environment. Let’s delve into the journey of a monolithic catalyst from production to disposal.
How are monolithic catalysts produced?
Monolithic catalysts are produced using a precise process involving several stages. Firstly, the monolith substrate is made from a ceramic or metallic material, designed to be both durable and chemically stable. This is then coated with a washcoat containing the active catalyst material, typically a metal or metal oxide.
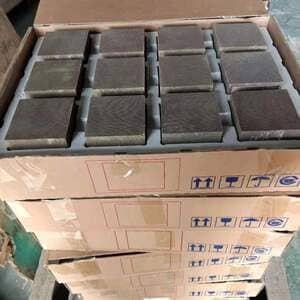
How long does a monolithic catalyst typically last?
The lifespan of a monolithic catalyst can vary widely depending on the specific application and operating conditions. Generally, these catalysts are known for their durability and can last for several years under normal operating conditions. However, factors such as extreme temperatures or impurities in the feed can potentially shorten their lifespan.
What is the impact of monolithic catalysts on the environment?
Monolithic catalysts, due to their high efficiency and long lifespan, can reduce the environmental impact of industrial processes by effectively converting harmful pollutants into less harmful substances. However, like any industrial product, they also have a potential environmental impact at the end of their life, when they need to be disposed of.
How are used monolithic catalysts disposed of?
At the end of their life, monolithic catalysts can be treated in several ways. In many cases, they can be regenerated, meaning that the catalyst material is restored to its active form, and the catalyst can be reused. If regeneration is not possible, the catalyst can be recycled, with valuable materials such as precious metals being recovered. In cases where neither regeneration nor recycling is possible, the catalyst may need to be disposed of as industrial waste, following strict environmental regulations.
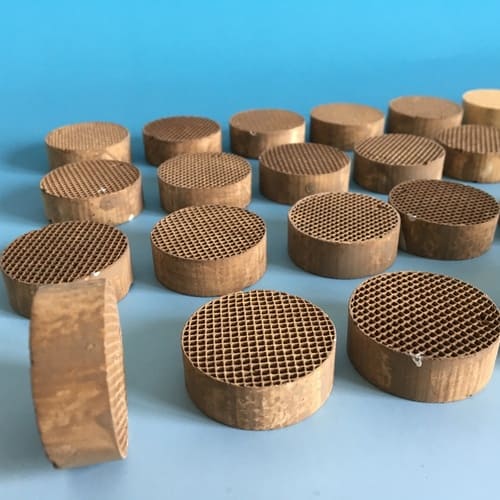
Conclusion
In conclusion, the lifecycle of a monolithic catalyst from production to disposal involves a series of carefully controlled steps. Each stage of the lifecycle is designed to maximize the performance and lifespan of the catalyst, while minimizing its environmental impact. By understanding this lifecycle, we can appreciate the sustainability and efficiency of monolithic catalysts and their important role in industrial processes.For further information about the lifecycle of monolithic catalysts, refer to this comprehensive study published in Applied Catalysis B: Environmental.