Have you ever wondered how large-scale manufacturers maintain the quality of essential components like Silicon Carbide Diesel Particulate Filters (DPFs)? What measures do they take to ensure that every unit meets the stringent standards required for efficient operation? When procuring these components in volume, how can you be confident in their quality and reliability?
The importance of stringent quality control in Silicon Carbide DPF procurement cannot be overstated. These components play a crucial role in reducing emissions and enhancing the performance of diesel engines. High-quality DPFs not only comply with regulatory standards but also offer durability and efficiency. In volume procurement, where the stakes are even higher, ensuring consistent quality across large batches becomes crucial.
Maintaining interest in this topic is vital, especially for stakeholders in the automotive and industrial sectors. Understanding quality control measures can significantly impact operational efficiency and compliance with environmental regulations.
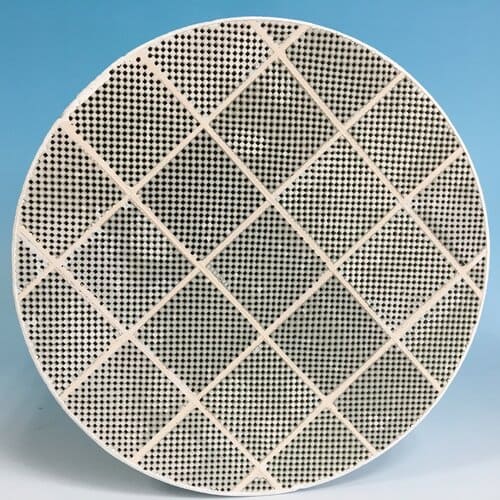
What Are the Key Quality Control Measures for Silicon Carbide DPFs?
Quality control in Silicon Carbide DPF manufacturing is a multi-layered process. It begins with the selection of raw materials and extends through manufacturing, testing, and final inspection.
- Material Quality: The quality of Silicon Carbide used in DPFs is paramount. Manufacturers must source high-purity materials to ensure the filter’s durability and effectiveness in trapping particulates.
- Manufacturing Process Standards: Adhering to strict manufacturing protocols is crucial. This includes precise control of temperatures and pressures during the sintering process, which impacts the structural integrity of the DPF.
- Testing Protocols: Rigorous testing is essential. This includes pressure drop tests, thermal shock resistance, and filtration efficiency assessments.
- Batch Consistency: In volume procurement, consistency across batches is a major concern. Statistical quality control methods can be employed to monitor and maintain uniformity in large-scale production.
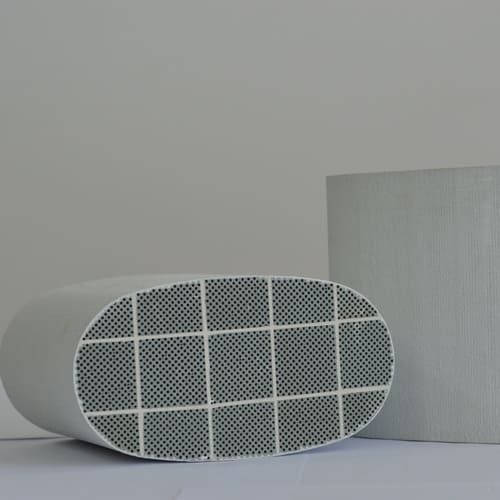
How Do These Measures Impact DPF Performance and Durability?
Quality control directly influences the performance and durability of Silicon Carbide DPFs. A well-manufactured DPF will have:
- High Filtration Efficiency: Effectively trapping particulates without causing excessive back pressure on the engine.
- Thermal Resistance: Crucial for withstanding the regeneration process, where temperatures can spike significantly.
- Mechanical Strength: Ensuring the DPF can endure the vibrations and stresses of a running engine.
What Are the Challenges in Quality Control During Volume Procurement?
Volume procurement poses unique challenges:
- Maintaining Consistency: Ensuring every unit in a large batch meets the same quality standards.
- Scalability: Scaling up production without compromising quality.
- Supplier Reliability: Finding and maintaining relationships with suppliers who can consistently deliver high-quality materials.
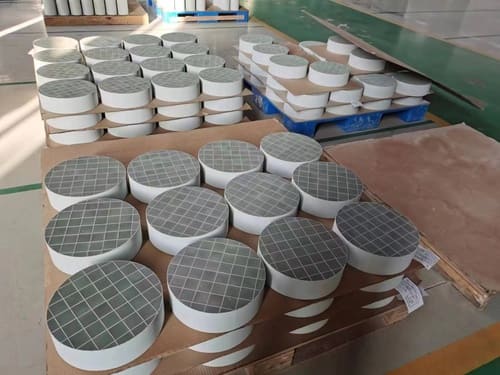
Conclusion
Quality control in the procurement of Silicon Carbide DPFs is a critical factor that influences not only the performance of the filters but also the overall efficiency and compliance of diesel engines with environmental regulations. By focusing on material quality, manufacturing standards, rigorous testing, and batch consistency, manufacturers and buyers can ensure the reliability and effectiveness of their DPFs. Understanding these measures is key for stakeholders in the automotive and industrial sectors, especially when dealing with large-scale procurements.