What if there were a technology that could transform harmful pollutants into harmless substances? What if this technology had the potential to significantly reduce emissions and contribute to a cleaner environment? Monolithic catalysts are one such innovative solution. But how can we ensure these tiny powerhouses continue to perform at their best? What are the best practices for maintaining monolithic catalysts to ensure their optimum performance and longevity?
Maintaining monolithic catalysts requires more than just periodic check-ups; it’s about understanding their needs and providing the right environment for them to thrive. By following a few best practices, industries can ensure that these catalysts consistently deliver their pollution-fighting potential, leading to cost savings and environmental benefits.
In this blog post, we will explore the key practices to keep monolithic catalysts in top shape, maximizing their efficiency, and contributing to a sustainable future.
How can industries monitor the condition of monolithic catalysts?
Regular monitoring is essential to ensure the optimal performance of monolithic catalysts. Techniques such as catalyst activity testing and fouling analysis help assess the catalyst’s health and identify any potential issues. Monitoring can help detect early signs of deactivation or degradation, allowing for timely corrective measures to be taken.
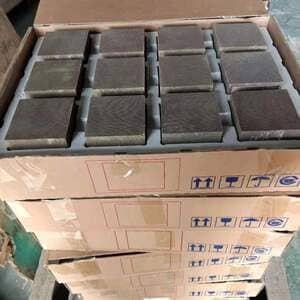
What preventive maintenance measures can be taken?
Preventive maintenance is crucial for prolonging the lifespan of monolithic catalysts. Regular inspection and cleaning of the catalyst surface can prevent the build-up of deposits and particulates, which can hinder catalytic reactions. Additionally, proper catalyst regeneration procedures can help restore the activity of a deactivated catalyst, extending its useful life.
How can industries optimize operating conditions for monolithic catalysts?
Optimizing operating conditions is vital for ensuring the best performance of monolithic catalysts. Maintaining proper temperature, pressure, and flow rates within the recommended ranges can enhance the catalyst’s efficiency and prevent damage from harsh conditions.
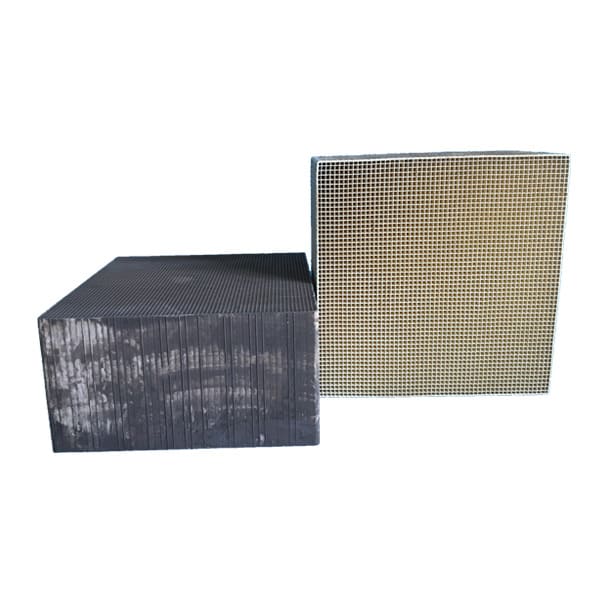
How can catalyst poisoning be prevented?
Catalyst poisoning, where the active sites of the catalyst are blocked or deactivated, can significantly impact performance. Implementing filtration and purification systems to remove potential poisons from the feed stream can help prevent catalyst poisoning and maintain its effectiveness.
Conclusion
In conclusion, maintaining monolithic catalysts is essential to ensure their optimum performance and extend their useful life. Regular monitoring, preventive maintenance, and optimized operating conditions are critical to keeping these catalysts in top shape. By adhering to best practices, industries can unlock the full potential of monolithic catalysts in reducing emissions and promoting a cleaner, more sustainable future.
For further information and resources on maintaining monolithic catalysts, you can refer to this research published in ScienceDirect.