Have you ever wondered how your vehicle’s diesel particulate filter (DPF) manages to survive the inferno inside the exhaust system? Or why, despite the scorching temperatures, it doesn’t just melt away? The answer lies in the material magic of Cordierite DPFs. But what makes cordierite so special, and how does it resist such extreme heat?
Cordierite, a ceramic material used in DPFs, is renowned for its exceptional heat resistance. But why is this important? Well, DPFs are crucial components in modern diesel engines, tasked with capturing and eliminating soot particles from exhaust gases. This process involves periodic regeneration phases where temperatures can soar. Thus, understanding the heat resistance of cordierite DPFs is crucial for both vehicle manufacturers and environmentalists.
Keeping you glued to this article isn’t just about the high temperatures – it’s about unraveling the mysteries of a material that plays a pivotal role in keeping our air clean.
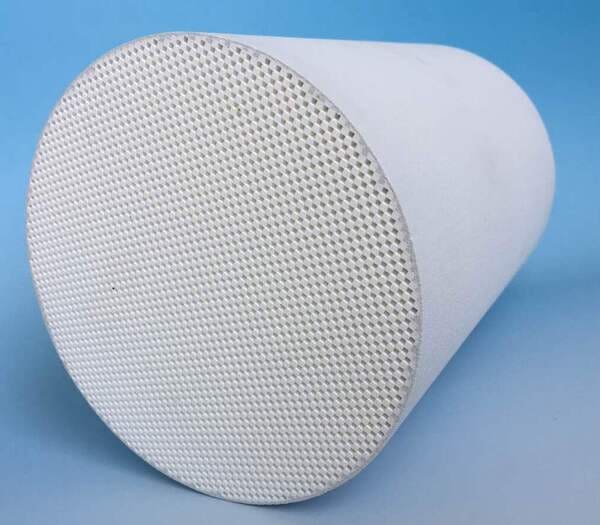
What Makes Cordierite DPFs Resilient to High Temperatures?
Why does cordierite, unlike other materials, stand up so well to the searing heat of exhaust gases? The secret lies in its unique crystalline structure and composition. Cordierite, a silicate of magnesium, aluminum, and iron, has a low coefficient of thermal expansion. This means it doesn’t expand much when heated, reducing the risk of thermal stress and cracking under extreme temperature fluctuations.
Furthermore, cordierite has a relatively high melting point, typically around 1475°C (2690°F). This is significantly higher than the temperatures typically reached during the regeneration process in DPFs, which can range from 600°C to 1200°C (1112°F to 2192°F). This high melting point ensures that the DPF maintains its structural integrity even under intense heat.
What Challenges Do High Temperatures Pose to DPFs?
The primary challenge for any DPF material, including cordierite, is to withstand the thermal stress during the regeneration phase. This phase is essential for burning off the accumulated soot particles. However, it subjects the DPF to periodic episodes of extreme heat.
Another challenge is the long-term durability of the DPF. Over time, repeated heating and cooling cycles can cause wear and tear on the material, potentially leading to cracks or failures. This is where the thermal stability of cordierite becomes a significant advantage, ensuring longevity and reliable performance.
How Do Cordierite DPFs Compare to Other Materials?
Cordierite isn’t the only material used in DPFs. Silicon carbide (SiC) DPFs are another popular choice, known for their superior thermal conductivity and mechanical strength. However, cordierite DPFs have the edge when it comes to cost-effectiveness and a lower environmental impact during manufacturing.
While SiC can better withstand higher temperatures and has a longer lifespan, cordierite DPFs offer a more economical solution, especially for light-duty vehicles. The choice between the two often boils down to the specific requirements of the vehicle and the balance between cost and performance.
Conclusion
Cordierite DPFs are marvels of material science, perfectly adapted to the hostile environment of a vehicle’s exhaust system. Their ability to withstand high temperatures without melting or degrading is crucial in maintaining efficient engine performance and reducing environmental pollution. As we continue to seek sustainable solutions in automotive technology, understanding and improving materials like cordierite remains a key focus. In the end, it’s not just about enduring the heat – it’s about contributing to a cleaner, greener future.
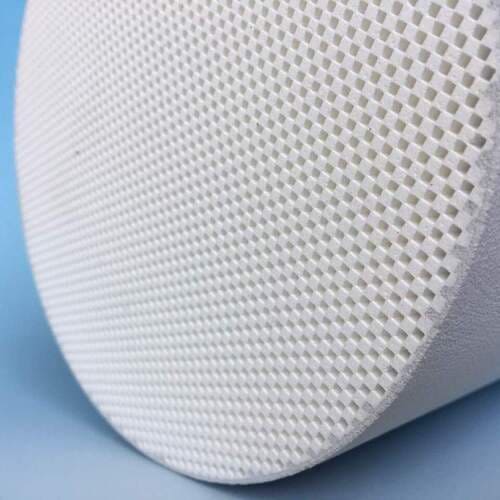