The performance-related and efficient features are rapidly industrializing with monolithic catalysts. But how do you have them installed correctly and how do you operate them effectively? What does one have to do in order to reap maximum benefit from the advanced catalytic systems? This guide clearly outlines your way to installation and operation by guaranteeing optimized performance with reliability. Long-lasting results.
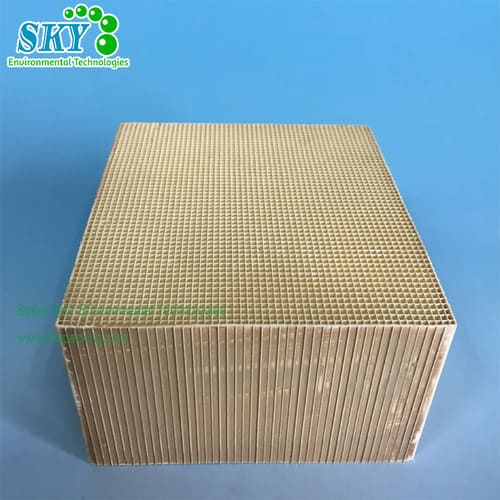
What are monolithic catalysts?
Monolithic catalysts are solid structures, basically of a honeycomb-like geometry, usually fabricated from ceramic materials such as cordierite. The advantages of monolithic catalysts compared to traditional powdered catalysts are low pressure drops, high mechanical strength, and good mass transfer efficiency. Their structure provides large surface area for catalytic reactions with minimum resistance to the gas flow. Therefore, this kind of catalyst is very suitable for such a great variety of applications: emissions control, chemical processing, and energy production.
Why Monolithic Catalysts?
Monolithic catalysts have been considered superior to all other forms due to the durability, efficiency, and wide applicability of the catalysts in various reactions. They are very important in industries that require stringent emission control standards. The proper selection of catalysts ensures enhanced production, reduced energy consumption, and adherence to environmental regulations.
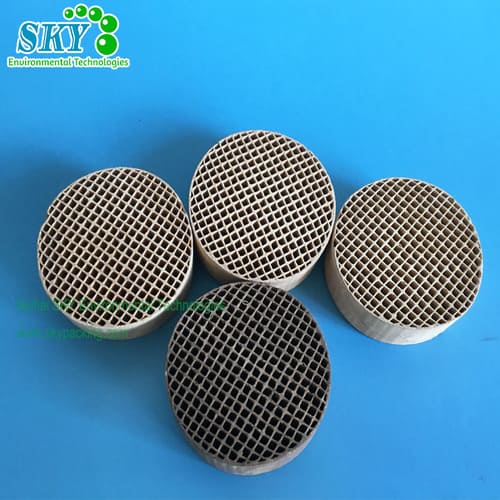
Some Questions to Address When Installing Monolithic Catalysts
- How do you prepare for the installation of catalysts?
- What are the factors that can affect operational efficiency?
- How would you ensure consistent performance over time?
1.Installation Preparation
Preparation is one of the most significant keys to the successful installation of monolithic catalysts. Here’s what you need to do:
A. Choose the Right Catalyst
A monolithic catalyst shall be selected as per your application. Examples of Noble Metal catalysts are excellent for CO oxidation, while other formulations are for NOx or VOC reduction. Recommend from appropriate studies or manufacturers.
B. Design Parameters Analysis
Mechanical strength, thermal stability, and operating condition compatibility tests shall be performed. It is supposed not to deteriorate with high temperatures and the pressure of gas flow.
How Catalyst Is Prepared
Source: De Gruyter – Catalyst Design
C. Preparation of Surface Coating
Coating, if it may be necessary, with approaches like dip-coating and sol-gel techniques. The homogeneous coating ensures a greater performance factor and doesn’t create hot spots.
Source: MDPI – Coating Techniques
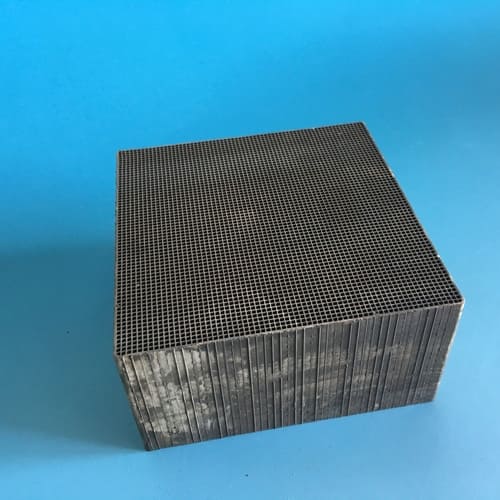
2. Installation Procedure
Good installation ensures it yields this designed performance as elaborated on below:
a. Catalyst Mounting
Fasten the monolith within the reactor or exhaust system; it shouldn’t shift during operations as this results in mechanical failure or complete loss of efficiency.
b. Temperature Measurement
Position sensors at both the inlet and exit to the reactor for measuring temperature. Temperature needs to be kept stable as fluctuation would cause reduced efficiency of catalysts or lowered rates of reaction.
Source: PMC – Effects of Temperature
c. Optimization of Gas Flow
Improve gas distribution by using either diffusers or flow adjusters to avoid dead zones that will reduce reaction efficiency.
Source: De Gruyter – Flow Optimization
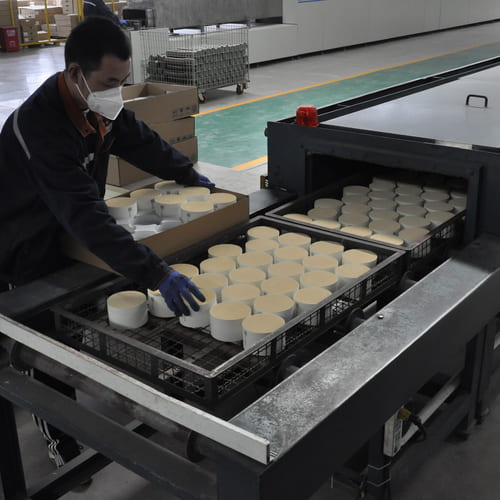
3. Operating Conditions
Optimal operating conditions will maintain catalyst activity over long periods.
a. Temperature Control
Operate at an optimal temperature. For example, the optimal working temperature of CO oxidation over noble metal catalysts is in the range of 200–300 °C. The operation temperatures should not be too high to avoid sintering or deactivation.
b. Gas Composition
Monitoring of the composition of the inlet gas mixtures is performed on a regular basis; sudden variations can affect either the conversion rate or selectivity.
c. Pressure Drop Monitoring
Monitor increasing pressure drops: these can indicate blockages or fouling.
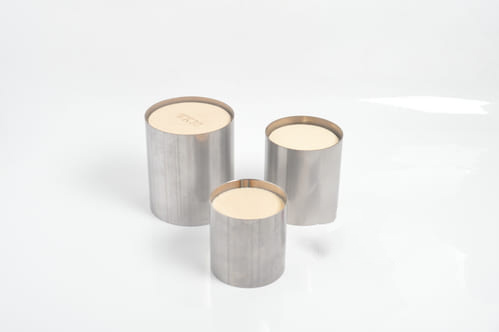
4. Performance Testing
Regular performance testing is highly important:
a. Activity Testing
Measure the rates of conversion and product selectivity: for example, combustion of methane on a monolithic catalyst may have an efficiency of over 99% under optimum conditions.
b. Stability Monitoring
Check for long-term stability. Frequent checks enable problems such as sintering or poisoning to be detected early.
Source: PMC – Stability Research
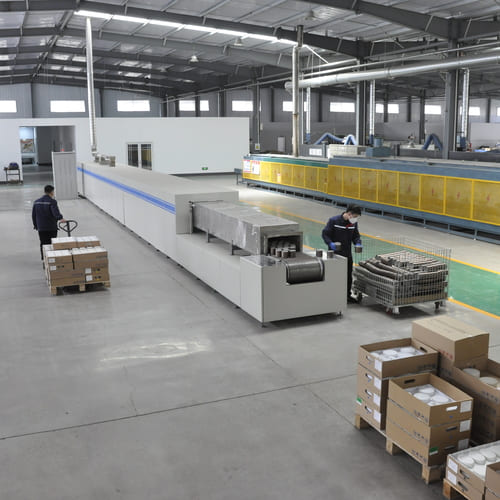
5. Maintenance and Troubleshooting
a. Cleaning Procedures
Clean the catalyst periodically by removing blockages to offer a free passage to gases either by thermal treatment or by chemical wash.
b. Replacement Schedules
Establish periodic replacement schedules from given performance indicators or from available data of life cycle.
c. Eliminate Common Problems
The efficiency drop or pressure rise is generally a symptom of either mechanical damage or fouling, thus should be investigated and eliminated.
Conclusion
Monolithic catalysts offer a number of benefits when it comes to industrial processing, including efficiency, longevity, and high performance. Proper installation and operation will let the full benefits of this type of catalyst be realized. By following this guide, you can ensure optimal performance, meet emission standards, and contribute toward sustainable industrial practices.